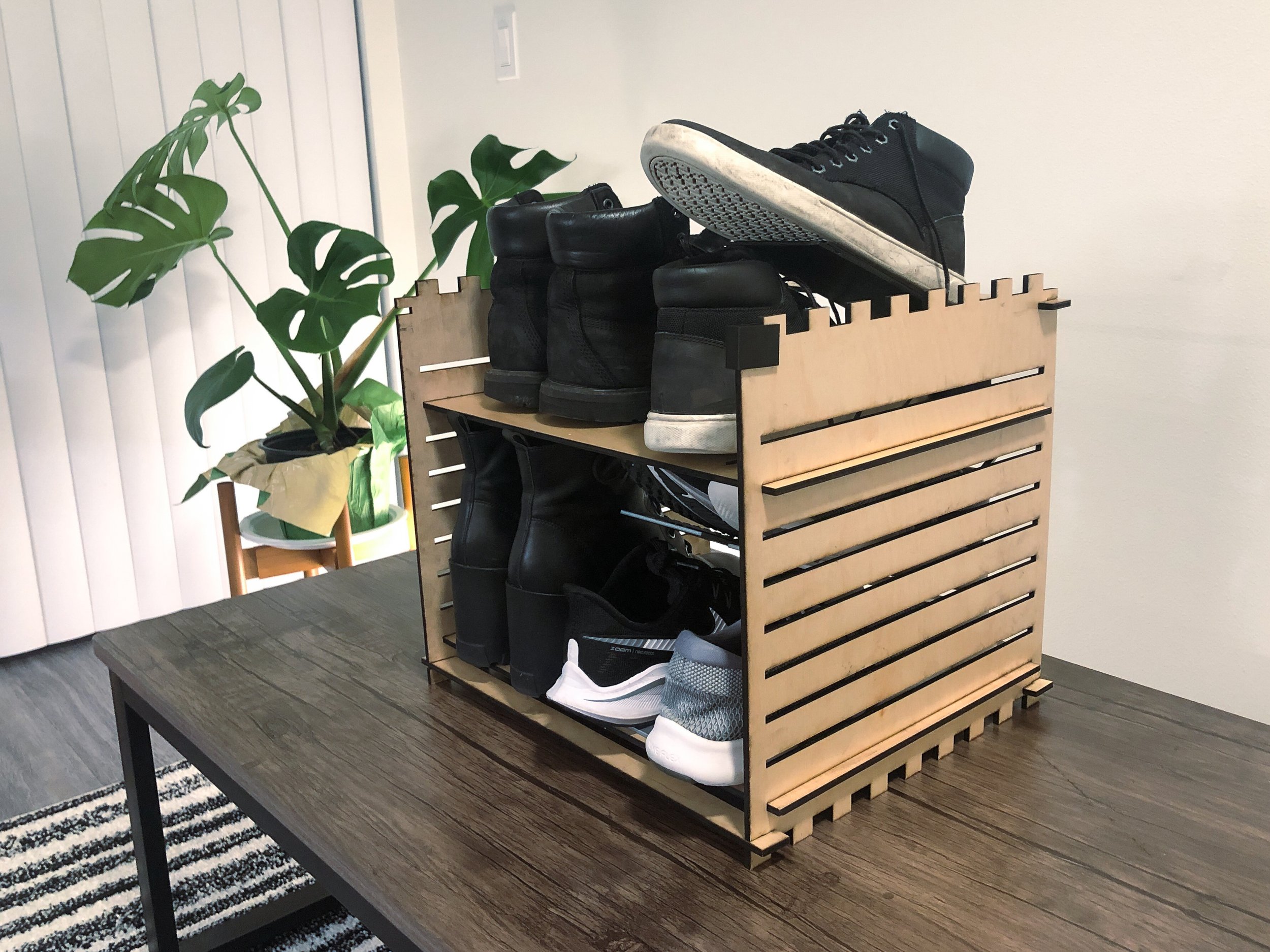
Shoe Rack & Shoe Stacker
I created a stackable laser-cut shoe rack and a 3D-printed shoe stacker.
I wanted to create something functional that would make my personal space more organized and efficient. I was also interested in creating something that others could easily recreate and utilize by downloading my openly available Illustrator and STL files (access everything on my GitHub).
December 2021
1 Week
Solo Project
Designer
Digital Fabrication, 3D Printing, Laser-Cutting, SolidWorks, Video Film & Editing
Date
Duration
Team
Role
Skills
SEE THE PROCESS —
Designing and prototyping two storage devices: a shoe rack and shoe stackers.
PROJECT GOALS: 3D-PRINTED SHOE STACKER | STACKABLE LASER-CUT SHOE RACK | USER TESTS | VIDEO
Key Design Decisions
The shoe rack must be shelf-height adjustable. Shoes come in different sizes and heights.
The shoe rack must be stackable. When more storage is needed, users should be able to cut another rack and place it on top of the previous one. No modification to the rack’s design should be needed.
The shoe stacker should be compatible with different types of shoes. Greater compatibility with different shoes makes the design more versatile and applicable to the user’s closet.
The shoe stacker should print without support material. Reduce material waste and printing time.
The shoe stacker should fit in the shoe rack. Both devices should work together!
Sketches & Preparation
I began with a few initial sketches of my devices to illustrate what I had in mind.
Idea Sketches
I took measurements of my space and shoes to get an estimate of how big the shoe rack and shoe stackers should be. After, I sketched more final versions of both the shoe rack and stacker in my sketchbook with rough dimensions. From there, I began working on the CAD model for the shoe stacker.
3D-Printed Shoe Stacker
I modeled the shoe stacker in SolidWorks, splitting the device into two parts, the stacker and the anti-slip patch that would be glued to the top of the stacker, to eliminate the need for support material.
Shoe Stacker CAD
Anti-Slip Patch CAD
3D-Printing
The 3D-printing process was approximately 9 hours of printing in total for both parts. The stacker printed without issue, but I ran into a few bed plate adhesion issues with the anti-slip patch and realized that my silver PLA filament wouldn’t print the model properly. I fixed the bed plate adhesion issue by printing one patch at a time instead of two and switching to another PLA filament roll. On my first test print of the anti-slip patch, the circular grippy components would fall off the base. This was resolved by increasing the base’s thickness in the CAD model.
Anti-Slip Patch Failed Print
I used tape to secure the patch onto the stacker, and then tested for durability by inserting my heaviest shoes into the stacker. The stacker did not break and shoes did not slip off the top. From there, I repeated the above prints twice to have 3 stackers in total. The stackers can stack into each other to save space.
Shoe Stackers
Shoe Stackers Stacked Into Each Other
Laser-Cut Shoe Rack
The shoe rack was the most challenging part of my project.
I first designed how the shoe rack would stack. The top of the shoe rack must allow the bottom of another shoe rack to sit on top. Designing in Illustrator, I created notches on the top and bottom edges of the side legs. These notches would fit together when stacked and would be secured with a clip. I made the shoe rack shelf-height adjustable by creating 9 different slots where the user could insert 1 or 2 shelves.
Shoe Rack Side Legs
Variety of laser-cut and 3D-printed clips tested
My goal was to laser-cut all components for the rack, so I created a number of clips to test. I needed two kinds of clips: ones to secure the shelves in place and ones to connect stacking racks. After testing, I realized that laser-cutting was a poor choice for making clips, because the edges of the material wear down over time, making the fit too loose. I resolved this issue by modeling and 3D-printing the needed clips. Once all parts were cut/printed, I began assembling the shoe rack.
Assembly
Once assembled, I realized the shoe rack wasn’t sturdy; it would sway back and forth. I resolved the wobble by cutting the side leg pieces to include a notch along the left and right edges at the top and bottom. I placed laser-cut bars at these notches that would connect both side leg pieces and used the cut-out wood from the slots to create cross bars on the back of the rack. The cross bars would be held in place by 3D-printed clips as shown below. These temporary changes made the shoe rack sturdy, and now it was complete.
Shoe Rack with Cross Bars
Two Shoe Racks Stacked
Video Demo
Before filming the video, I made a checklist of things I wanted to include and then storyboarded it. Filming was straightforward, and the editing was done in Adobe Premiere Pro.
Video Planning
Storyboarding
Evaluation & Testing
In addition to receiving critiques from my peers in class, I conducted one user test with a neighbor in my apartment building. I focused on testing the usability of both organizer tools and encouraged the user to think aloud.
3D-Printed Shoe Stacker
I wanted to evaluate whether it could withstand the weight of different kinds of shoes without breaking, hold shoes in place without slipping, and see how well it fits on the shoe rack. This was tested by having the user insert each of their shoes in the 3 stackers I provided and having them place the stackers on and off the shoe rack.
Laser-Cut Shoe Rack
I wanted to evaluate how easy it was to assemble, how many shoes it could hold on each tier (with and without stackers), and how sturdy it is. To do this, I had my user assemble the shoe rack, change shelf height, stack another shoe rack on top of the first one, and comment on overall sturdiness.
User Testing Feedback and Critique
Here is the feedback I received as I worked on this project and during the final showcase.
3D-Printed Shoe Stacker
4/4 pairs of the user’s shoes were successfully held without stacker breakage.
Withstanding weight of different shoes
Holding shoes in place without slipping
3/4 pairs of the user’s shoes held onto the stacker without slipping.
Fits on shoe rack
4/4 pairs fit on the shoe rack.
Laser-Cut Shoe Rack
User said that the shoe rack is difficult to assemble because the shelves don’t slide easily into the slots. They mention that installing the crossbars in the back is confusing, because there is not a clear place to put them. They gave assembly a 1/5 rating for ease of assembly (1 being very difficult and 5 being very easy).
Ease of assembly
Each shelf can hold 2 pairs of shoes without stackers and 3 pairs with stackers. The user’s shoes are larger than mine, so both pairs might not sit flat on the shelf.
Shoe storage
User moved one shelf into another slot and said that it was annoying to switch out since the slot fit is too tight. They mention that they would likely determine their shelf height before using the rack and then keep shelf height as is after assembly to avoid having to change shelf height.
Changing shelf height
The user easily stacked the second shoe rack on top of the first one with no issue.
Stacking shoe racks
Without the crossbars in the back, the shoe rack is very wobbly. It could still hold items on the shelves, but the user wouldn’t put anything valuable on the rack in case the rack falls over. The shoe rack is much sturdier when the crossbars in the back are installed.
Comments on sturdiness
General Comments from the User Test
There should be a ledge that prevents shoes from falling off of the shoe stacker.
The user would like to remove a stacker from the rack without having to touch the sides of their shoe.
Crossbar installation on the shoe rack should be made more clear.
The clips to connect stacking shoe racks should be a tighter fit so that the user can lift up the shoe rack from the top rack.
Overall, the shoe rack is nice and provides a good place to store things.
Feedback from Design Peers
“Instead of changing the model of the stacker, you can model clips to attach on the sides.”
“Shoes might slip out of the bottom when you remove the stacker from the rack so think about adding an anti-slip patch to the bottom of the stacker too.”
“I would totally use this! Could you forward me the files?”
The overall message from feedback is to make the shoe rack easier to assemble and to ensure that shoes don’t slip off or slide out of the stacker.
Analysis
What Worked Well
Both prototypes are functional!
The shoe stacker prints without support material.
People that saw the shoe stacker said that they would use it.
3D-printed clips are much more successful than laser-cut clips. The print offers greater flexibility.
The shoe rack is capable of holding a lot of items and is very sturdy when stabilized with cross bars.
What Needed Improvement
The shoe rack could be easier to assemble.
Next Time: I would cut the slots to be larger so that the shelves slide in more easily. I would also redesign the shoe rack to include permanent crossbars (the current crossbars are a temporary solution) and indicate where they would be installed with engravings.
The shoe stacker could grip onto the shoes better so that they don't slip.
Next Time: I would add an anti-slip patch to the bottom portion of the stacker, and I would remodel the stacker to include a ledge on top to prevent the shoe from slipping off the stacker. I would also model and print clips to attach to the sides that would allow the user to pull out the stacker more easily from the shoe rack.
Reflection
In the future, I’ll work on checking my design for any potential structural issues prior to prototyping to prevent wobbling. If I had more time, I would have revisited the design to improve the structure. I would also allocate more time for issues that may arise during the prototyping process. I allocated 10 hours outside of class to work on making the prototypes but spent closer to 15 hours prototyping. Video filming and editing also took a bit longer than expected.
Overall, I’m proud of what I was able to create and accomplish during this one-week project, especially since I was recovering from a major injury at the time. It was fun, and I’m glad about the new storage space!
Want to create the Shoe Rack & Shoe Stackers?
All files can be found on my GitHub!
ON THE PLAYGROUND: DISCO BALL STAND | MINI TABLETOP BOWLING GAME | KIRBY | APPLYING UX TO MY LIFE